$ 0.035 0.94%
Recycling Regeneration Chain (RRC) Rank 4453
Mkt.Cap | $ 0.00000000 | Volume 24H | 0.00000000RRC |
Market share | 0% | Total Supply | 1.8 BRRC |
Proof type | N/A | Open | $ 0.03 |
Low | $ 0.03 | High | $ 0.04 |
Rethinking plastic packaging – towards a circular economy
The artefacts utilized in our work were post-consumer public telephone weather protector caps, which, in Brazil, are manufactured with a composite of unsaturated polyester/glass fibre. Although we used this specific artefact, the methodology can be extended to different types of post-consumer materials or industrial scraps.
Treatment of milled SMC with ethanol/potassium hydroxide at 85°C for 48 h ultimately affords a soluble polymeric fraction, consisting of styrene–fumaric acid copolymers. The excess of potassium hydroxide as well as the filler are removed via a neutralization step, which results in a large stream of waste chemicals. Treatment of SMC chips with ethanolamine at 180°C for 48 h gives a reaction mass that can be split into three fractions, viz., the glass fibers, the filler, and a methanol-soluble polymeric residue. The excess of ethanolamine is recovered by distillation at 220°C and reduced pressure. The polymeric fraction consists of terpolymers of styrene, N,N′-di(2-hydroxyethyl)fumaramide and N-2-hydroxyethylmaleimide monomer units, the latter two bearing two and one hydroxyl groups, respectively.
A first attempt to measure the success of circular economy implementation was done in a construction company.[59] The circular economy can contribute to creating new posts and economic growth [60]. According to Gorecki [61], one of such posts may be the Circular economy manager employed for construction projects.
Glass-Fiber Reinforcement as a Means of Recycling Polymers from Post-Consumer Applications
Plastics are essential to modern life, though environmentalists and NGOs have also long warned of the impact that plastic waste has on land, water, and air. Today, regulators, industries, and society alike recognize the need to limit waste and identify solutions.
It was possible to cleave an epoxy resin crosslinked with phthalic anhydride with a yield of more than 99 wt.% soluble products at a temperature of 340°C in 2 h. First the thermally most labile bonds in the resin suffer homolysis, then the radicals formed that way are saturated by abstraction of hydrogen from the hydrogen donor. The most important reaction products like phenol, p-isopropylphenol and phthalic anydride were quantitatively analyzed by gas chromatography. This method also worked with a technical epoxy resin sheet reinforced with glass fiber mats and covered with copper foil.
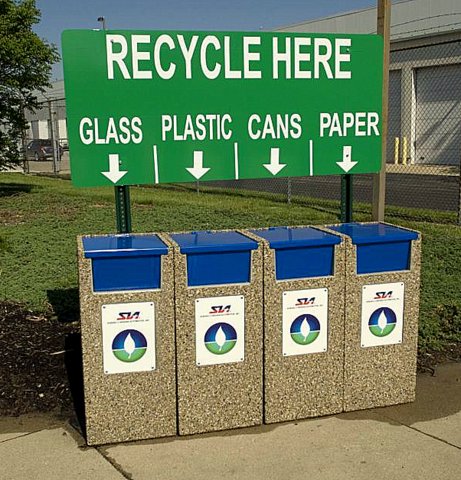
By 2020, it aims to develop robust ‘Design for a Circular Economy’ guidelines for both flexible packaging and the infrastructure to collect, sort and recycle. And by 2025, it aims to develop a collection, sorting and reprocessing infrastructure for post-consumer flexible packaging across Europe.
Results are discussed in terms of microstructural details, which include resin molecular weight and fiber length and orientation. Needs for recycling thermoset composite materials are considerably increasing. Unfortunately, such materials are particularly difficult to recycle due to their crosslinked nature. In this paper, we focus on the case of Sheet Moulding Compounds (SMC), which consist of an unsaturated polyester filled with glass fibres and calcium carbonate.
WRAP and the circular economy
A pyrolysis operator could expect to achieve a profit margin of almost $130 a ton, or nearly 30%. But Seine-Maritime generates only about 150 to 190 tons of municipal solid waste (MSW) a day, most of which (110 to 160 tons) goes to incinerators or landfills. To ensure sufficient supply for a 30-kT/y plant, an operator would need to either look beyond the Seine-Maritime province for supply or use plastics extracted from landfills, which would require cleaning and sorting. Depending on the mix of inputs, the output from pyrolysis is 70% to 80% oil, which can be used for a variety of purposes, and 10% to 15% gas, which is usually recycled to provide the pyrolysis heat.

The shift to a circular economy means using less virgin material and more recycled inputs, reducing a company’s exposure to ever more volatile raw materials prices and increasing resilience. The threat of supply chains being disrupted by natural disasters or geopolitical imbalances is reduced because decentralised operators provide alternative materials sources. Land degradation costs an estimated USD 40 billion annually worldwide, without taking into account the hidden costs of increased fertiliser use, loss of biodiversity, and unique landscapes.
To help create an end market for this material, we also committed to increase the recycled plastic content in our packaging to at least 25% by 2025. Decoupling our growth from our environmental impact is at the heart of our Unilever Sustainable Living Plan targets to reduce the weight of our packaging by one third by 2020 and halving the waste associated with the disposal of our products by 2020. Cheap, flexible and multipurpose plastic has become the ubiquitous material of today’s fast-moving economy. One area of direct concern for Unilever is the fact that just 14% of the plastic packaging used globally makes its way to recycling plants, and only 9% is actually recycled.1 Meanwhile, a third is left in fragile ecosystems, and 40% ends up in landfill. Every minute the equivalent of one rubbish truck of plastic leaks into streams and rivers, ultimately ending up in the ocean.
All Data You May Need about Recycling Regeneration Coin Perspectives and Cost
The circular economy appears as a helpful solution to diminish the environmental impact of the industry. This model significantly changed the previous business model of using disposable goods and oppositely, used good and materials can be regenerated fully and can be consumed again. This means that resources are upcycled and used again as well as manufactured goods so nothing is going to be called as a waste and dumped in the dumpsters rather then will be given a second life in different forms. If properly addressed, this could help retain valuable resources and materials within the EU economy as well as create sustainable economic and employment impacts.
In addition, much of the packaging we currently rely on is flexible – including crisp packets and pet food pouches – which are made from multiple materials, adhesives and coatings that cannot be easily separated and recycled. To overcome this, CEFLEX– a consortium of European companies and associations representing the flexible packaging value chain, is working to develop robust design guidelines for both flexible packaging and the infrastructure used to collect, sort and recycle it. This means materials constantly flow around a ‘closed loop’ system, rather than being used once and then discarded.
For Europe, a circular economy development path could halve carbon dioxide emissions by 2030, relative to today’s levels across mobility, food systems, and the built environment. In addition, sector specific analysis indicates that the UK could reduce greenhouse gas emissions by 7.4 million tonnes per annum by keeping organic waste out of landfills. The aspiration to replace linear products and systems with circular ones is an enormous creative opportunity.
This work has been done in view of their possible inclusion in the revised Fertilising Products Regulation. Unilever, PepsiCo, Proctor & Gamble, Dow Chemical Company, Danone and Coca-Cola have joined forces to invest USD $100 million in the fund. The Fund aims to remove access to capital as a barrier to waste management development, recycling infrastructure and to support innovative solutions to the problem of ocean plastics.

- A circular economy favours activities that preserve value in the form of energy, labour, and materials.
- The mechanical and melt flow properties of the compounded polycarbonate, having as much as 50% impurity, were studied.
- In October 2018 at the Our Ocean Conference in Bali, we announced our participation in The Ocean Fund.
- In 2018, we used around 4,845 tonnes of post-consumer recycled (PCR) plastic in our packaging, such as high-density polyethylene (HDPE) and polyethylene terephthalate (PET) in our plastic bottles.
Higher land productivity, less waste in the food value chain, and the return of nutrients to the soil will enhance the value of land and soil as assets. By returning biological material back into the soil, the circular economy will reduce the need for replenishment with additional nutrients. Recovering all of the nitrogen, phosphorus, and potassium from food, animal and human waste streams globally could contribute nearly 2.7 times the nutrients contained within the volumes of chemical fertiliser currently used.
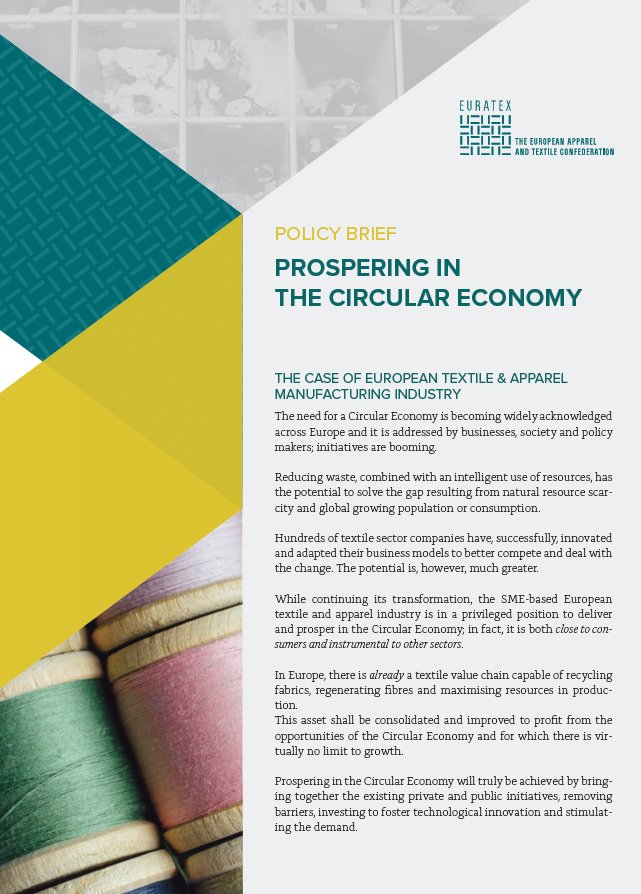
In 2018, we used around 4,845 tonnes of post-consumer recycled (PCR) plastic in our packaging, such as high-density polyethylene (HDPE) and polyethylene terephthalate (PET) in our plastic bottles. We expect our use of PCR materials to accelerate rapidly over the next few years as the design processes begin to deliver at scale. This will help us achieve our global commitment to include at least 25% recycled content in our plastic packaging by 2025. We aim to optimise materials each time we redesign our packaging or develop concentrated or compressed versions of our products. It can take significant investment and ingenuity to reduce the amount of material in a pack, even by just one gram.

The course of the solvolytic process is affected by the nature of the LPA and the original sizing of the glass fibers. In the present work, γ irradiation is used for the in situ compatibilisation of blends of recycled high density polyethylene (rHDPE) and ground tyre rubber (GTR) powder. The expected compatibilisation mechanism involves the formation of free radicals, leading to chain scission within rubber particles, crosslinking of polyethylene matrix and co-crosslinking between the two blend components at the interface. While uncompatibilised rHDPE/GTR blends show poor mechanical properties, especially for elongation at break and Charpy impact strength, irradiation leads to a significant increase of these mechanical performances. Such behaviour is attributed to the development of an adhesion between GTR particles and the surrounding thermoplastic matrix.

While these actions have yet to materially reduce the volume of waste, they have sent a clear signal that the status quo can shift rapidly. While plastics have myriad benefits, they also create a vast, global, and complex waste problem. Some estimates say that humans have manufactured more than 9 billion tons of plastics in the past century, and almost 7 billion tons have become waste. In recent decades, the rising middle class in emerging markets has sent production soaring; half of history’s plastics have been produced in the past 15 years. The UN predicts that under current consumption rates and waste management practices, approximately 12 billion tons of plastic waste will be dumped into landfills and leaked into the environment by 2050.

Project Summary
A significant improvement of the tensile modulus was found, namely after one washing of the fibers for the ionomer based composites and two washings for the LDPE based ones. The recycling of internal waste of poly(vinyl chloride) (PVC) and wood fibre-reinforced PVC composite was investigated and compared.

Closing the Loop with Chemical Recycling

This work was then extended by measuring the tensile strength of single fibers. An initial study of the residual strength of fibers processed in a fluidized bed was also undertaken by measuring the tensile strength of fibers recovered at two temperatures.
This means carefully considering the systems in which our products flow – and working with national governments to develop waste infrastructure. In October 2018 at the Our Ocean Conference in Bali, we announced our participation in The Ocean Fund. Managed by Circulate Capital, this cross-value chain investment fund is designed to accelerate the growth of waste collection and waste management in South and South-east Asia.
They are for example making designs of electric motors of which the magnets can be easily removed for recycling the rare earth metals. The paper provides an overview of the literature on Circular Economy (CE) theoretical approaches, strategies and implementation cases. After analyzing different CE approaches and the underlying principles the paper then proceeds with the main goal of developing tools for CE implementation.
Starting in India and Indonesia, the three-year agreement focuses on ways to develop and scale up collection and reprocessing infrastructure so that recycled content is channelled back into the value chain. Together, we will explore ways to build recycling capacity and develop new processes and business models. Recent progress in the recycling and recovery of polyurethane and polyurethane composites is reviewed. The various types of polyurethane waste products, consisting of either old recycled parts or production waste, are generally reduced to a more usable form, such as flakes, powder or pellets, depending on the particular type of polyurethane that is being recycled. The various recycling technologies for material and chemical recycling of PU materials have greatly contributed to improve the overall image regarding the recyclability of polyurethanes in recent years, by far the most important being regrinding and glycolysis.
Only 9% of plastic waste was recycled, 12% was insinuated and 79% (4.9 billion tons) were dumped in the dumping locations or wasted in environment. The JRC has produced the EU reference document for the management of waste from extractive industries (MWEI BREF). This document will help competent authorities when setting permit conditions for extractive waste facilities in the EU to ensure safety and lower the environmental impact from the management of waste from extractive industries. The document covers the management of extractive waste from all onshore extractive industries, from small quarries to large metal mines, and including oil and gas exploration and production. In this context, efforts are ongoing across the EU to develop manure processing technologies that allow manure to be turned into a safe and agronomically valuable resource that could be more widely used in NVZ.
The recycled fibers were used to prepare ‘new’ composites, i.e., they were incorporated in the same polymer matrix, but of virgin quality. This paper investigates the effect of such an interphase alteration on the tensile performance of these materials.